2024/2/18
brought to you in part by
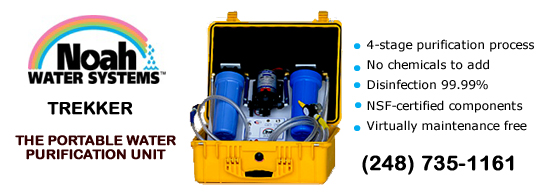
CREATING A CIRCULAR SUPPLY CHAIN FOR RARE EARTH ELEMENTS
Cleantech Group names Ontario start-up Cyclic Materials Early Stage Company of the Year on its Global Cleantech 100 for 2024
"North America needs a circular solution to the critical minerals and rare earth elements supply to power our sustainable future. We are incredibly grateful to have achieved this recognition, and hope that it will help continue to raise awareness about the importance of recycling critical metals, ensure a resilient, domestic supply chain to power our electric future and lead to new strategic partnerships.”
--Ahmad Ghahreman, CEO, Cyclic Materials
Interview with Ahmad Ghahreman, Co-founder, and CEO of Cyclic Materials
By Suzanne Forcese
WT: Congratulations on being recognized by Cleantech Group as Early Stage Company of the Year! Cyclic Materials was also included in the Cleantech Forum North America Deal Book, Team Canada. Please introduce yourself to our viewers and give us an overview of Cyclic Materials.
Ghahreman: Thank you! Cyclic Materials is a cleantech company in the critical minerals and rare earth elements industry. Our advanced metals recycling technology takes end-of-life consumer products (such as automotive parts and MRI machines) and produces high-quality rare earth elements (REEs) and other critical materials (such as copper, aluminum, steel, cobalt, and nickel) necessary for the development of electric vehicles and other modern technologies.
WT: Please describe the journey that brought the co- founders together with your combined talents.
Ghahreman: I have worked in the metals recycling industry for many years. I earned my PhD at the University of British Columbia before joining the world’s largest gold mining company, Barrick Gold Corporation, as a metallurgist. Later, I joined the faculty at Queen’s University for eight years as a hydrometallurgy professor. There, I built the largest and most funded research team in the field in North America.
Before founding Cyclic Materials in 2021, I was an early co-inventor of Jetti Resources’ copper-mining extraction technology, now a $2.5B startup. As a technical consultant and advisory board member, I also led the technical side of the lithium-ion battery recycling company Li-Cycle in its infancy. The company went public on the NYSE at a $1.7B valuation.
My co-founder, Patrick Nee, is an MIT graduate, with an MBA from Columbia University. Patrick has a rich experience in building startups. Cyclic Materials is the 8th start-up for him.
I first met Patrick about 10 years ago on a copper project. Back in 2021, while discussing my vision to start Cyclic Materials, Patrick’s enthusiasm propelled him to join me in building the company. Currently, Patrick is our SVP of Strategic Partnerships and leads the company’s acquisition of feedstock and sale of products.
WT: What was the impetus to found Cyclic Materials?
Ghahreman: While working on a Li-Cycle project back in 2017, I learned that some metals and materials are critical both for electric vehicle battery manufacturing and magnets inside EV motors.
By 2021, EV sales were skyrocketing, yet the industry still depended on a limited supply of magnets from foreign countries.
My interest in magnet recycling grew further when I discovered that about 99% of viable REEs are discarded into landfills as waste, making rare earth elements in magnets among the least circular metals on our planet.
REEs are among the most critical metals in our world. The mining process to extract those metals is very carbon intensive.
Throwing those metals away, instead of recycling them, was unacceptable to me. I was certain that the critical metals supply chain needed a recycled solution, and that was the moment I decided to found Cyclic Materials.
WT: What is the Team's mission?
Ghahreman: Our mission is to create a circular, domestic supply chain for rare earth elements and other critical minerals right here in North America.
WT: With the global market for magnet rare earth oxides forecast to increase three-fold by 2030, establishing new sources of rare earth elements will be critical to support the electrification of the economy across Canada, North America, and the world. What are the rare earth elements?
Ghahreman: Rare earth elements are a group of 17 elements that are a critical component of modern technologies, including wind turbine generators, solar panels, MRI units, electric motors used in many applications, electric vehicles’ traction motors and other clean technologies that will power the electric transition. One of the most important REEs is neodymium, which is critical to the development of powerful permanent magnets used in electric motors.
WT: Tell us about the demand for rare earth elements.
Ghahreman: Metals like REEs are a finite resource. They don’t grow from the Earth, so there are only two sources: mining new or recycling old.
China currently accounts for 63% of the world’s REE mining, 85% of REE processing and 92% of REE magnet production. The country recently banned the export of REE technologies, introducing new risk to this supply chain.
Plus, REEs are so good at what they do that it’s virtually impossible to replace them with other materials. Technologies like electric vehicles, wind turbines, robots and medical technologies will always rely on REEs—and these technologies make up booming industries with incredible staying power. As a result, we need to shore up a domestic, resilient supply of REEs to protect this interest in the future.
WT: What is Cyclic Materials' solution?
Ghahreman: Cyclic Materials’ recycling technology can recover mixed rare earth oxides, as well as other valuable minerals such as cobalt, nickel, copper, aluminum and steel from end-of-life (EOL) products. These materials can then be repurposed in new magnet technologies to power the electric transition and essential consumer technologies.
WT: Please describe your Mag-Xtract technology and hydrometallurgy technology.
Ghahreman: Cyclic Materials’ recycling technology is a proprietary process. What we can share is that our Mag-Xtract™ technology takes EOL products (such as electric motors, wind turbine generators and manufacturing waste) and isolates valuable magnet material.
This technology is unique from any other magnet recycling technology on the market because it can remove magnets from any kind of EOL product at scale. Magnet feedstock rarely contains just one type of magnet (it is typically a mix of four different magnet types). Our technology is magnet-type agnostic and can isolate magnets at any level of cleanliness.
Cyclic Materials’ recycling process is a two-part process that also includes proprietary hydrometallurgy technology. This technology recycles magnet feedstock processed by Mag-Xtract, as well as manufacturing waste, and uses a chemical process to convert it into mixed raw materials such as rare earth oxide, cobalt-nickel hydroxide, and other byproducts that can be repurposed for new magnet applications.
WT: Traditionally magnets have come from China...why is this problematic?
Ghahreman: Over 90% of rare earth magnets necessary for electric vehicle and wind power sectors are made in China. Depending on a single source for these crucial parts worries North American companies, business leaders and governments, as geopolitical events and tensions could significantly disrupt entire industries and derail sustainability goals.
The metals required to create these magnets are more often mined rather than recycled. The metals mining industry accounts for approximately 7% of worldwide GHG emissions and is rife with reports of human rights abuses from Malaysia to the Congo.
Mining destroys wildlife habitats, pollutes waterways and air and contributes to erosion and deforestation. The demand for mined materials essential to the electric transition does not justify the social and environmental consequences of the industry. Circular and ethical solutions, such as those introduced through Cyclic Materials’ technology, are needed.
WT: What is the Cyclic Materials’ footprint in your process?
Ghahreman: Cyclic Materials’ metals recycling processes carry less than 25% of the carbon footprint of traditional mining operations per Tonne of metal we produce. Plus, our process eliminates radioactive pollution and does not degrade land or disturb soil the way that traditional mineral extraction methods do. Our process also minimizes waste— 99% of viable REEs are currently discarded into landfills, trapped in e-waste like consumer technology and auto parts.
WT: How does this differ from traditional methods?
Ghahreman: Other REE recycling methods are not magnet agnostic, meaning they can only recycle separated, clean magnet feedstock. Because magnet feedstock rarely contains just one type of magnet (it is typically a mix of four different magnet types: neodymium, samarium cobalt, alnico, ferrite). This limitation dramatically reduces the volume of magnets other companies can process and recycle.
WT: How is the Cyclic Materials process revolutionizing and shifting perspective in the EV Industry?
Ghahreman: Cyclic Materials is shifting industry perspectives by building an independent sourcing network for critical metals and continually demonstrating the value of a circular supply chain.
Many stakeholders in the auto manufacturing and recycling industry understand the value and profit potential of accessing the metals within EV batteries such as lithium, nickel, and cobalt.
EVs have enormous value beyond battery materials. EVs and hybrid vehicles contain REEs that are small and lightweight and contribute to the performance and efficiency of the vehicles.
Additionally, EVs require two and a half times as much copper as internal combustion vehicles — a necessary metal for renewables, transmission & distribution infrastructure, and battery storage technologies.
Cyclic Materials’ unique, innovative recycling process allows auto manufacturers and recyclers to capitalize on the valuable materials within EVs and hybrid vehicles.
Our technology recovers REEs from end-of-life EV drive motors and hybrid transmissions. These materials are then reintroduced into the supply chain. Together, key players within the automotive sector will contribute to the sustainable management of resources and help develop local supply chains that address production shortages and mitigate the supply chain risk that currently exists due to heavy reliance on China as a source for critical components.
WT: Operating from your pilot facility in Kingston, ON, Cyclic Materials is processing feedstock at a capacity of 8,000 metric Tonnes per year. Why has Cyclic Materials chosen Kingston, ON?
Ghahreman: I used to live in Kingston so starting the company there was a quick way to get started. Currently, our head office is in downtown Toronto, and we will have operations across Canada and the USA. Soon, we will also have footprint in Europe and Asia as well.
Kingston is the “center of the universe” for critical mineral recycling companies. Not only is it a university town with a dense pool of talent, but it sits in the middle of an important corridor between Toronto, Ottawa, and Montreal, and is also close to the U.S. border. There is easy access to the highway, a large nearby water source, and train tracks for low-carbon shipping. All these really make Kingston an ideal location to start a business and grow. We are happy to call it Cyclic Materials’ home.
WT: Cyclic Materials' first facility was commissioned in September 2023. What can you tell us?
Ghahreman: In December 2023, we announced the opening and success of our new pilot plant. The design capacity of the plant is 1,000 kg/hour (8,000 Tonnes per year), and initial runs have processed several Tonnes of magnet feedstock per day. This plant scales our proprietary Mag-Xtract™ technology to near commercial size and is already producing magnet materials for us that could be recycled.
We are currently developing the first commercial demonstration plant for our Hydrometallurgy process that will process the recycled magnets produced in our pilot plant. This second plant will be commissioned in Q2 2024.
WT: Moving forward...what's next?
Ghahreman: At Cyclic Materials, we remain committed to creating a circular supply chain and growing our impact, aiding the energy transition. In the coming years, we will expand our presence with multiple facilities in North America, Europe, and Asia.
I am also pleased to announce some breaking news! We have expanded operations to accept two new feedstock streams: wind turbine generators and MRI machines. Through our strong partnership network, Cyclic has already sourced 37 MW capacity of wind turbine generators containing permanent magnets, and 116,000 pounds of MRI machines.
This development marks a strategic expansion for our company beyond automotive components and other permanent magnet-containing products into other end-of-life products.
|